The importance . and amount of electronics and software (SW) used in heavy vehicles is growing for every year. In order to meet customer needs of sustainable and reliable transports, very high requirements of reliability and robustness are necessary. In this very demanding truck environment, traditional component testing needs to be complemented with on-board software diagnostics and broad data collection from connected vehicles. In this way, real and potential failures can be detected very early on large fleets also then failure rates are relatively low.
The need for more robust electronics in heavy vehicles is driven both by customer demands for reliable transports and new technologies for reduced emissions and improved safety (1). In this paper these trends as well as reliability requirements for automotive electronics and the use of data collection from connected vehicles will be discussed.
Customer-driven heavy-vehicle development
Expectations of improved reliability and sustainable solutions for heavy-vehicles increase for every year. Simultaneously, the technical complexity of modern vehicles in terms of advanced electronic systems and software control continue to increase. For example, the number of sensors, control units and electrical actuators per vehicle typically grow with 5-10% annually.
Another important trend is that of transportation businesses focussing more on mastering logistics and serving their customers and less on vehicle maintenance. Leasing of trucks and long-term maintenance and service contracts offered by vehicles producers is becoming the norm. The traditional driver with long experience and solid technical knowledge of trucks is becoming less common. To a large degree modern heavy vehicles are expected to self-detect various real and potential failures and address them. In this way, severe damages in terms of vehicle standstill and costly repairs can be minimized.
Clearly, advanced electronics in combination with software development offers an opportunity to incorporate the complexity of modern heavy vehicles without jeopardizing reliability. Without advanced software functions and very robust electrical components, the needs for stringent emission control, high reliability and fuel savings would be impossible to meet.
The SW and electronics controlled vehicle
Superficially, a modern truck may seem to be quite similar to a 20-year-old truck, but below the surface an invisible technological shift has occurred. The modern truck or bus is equipped with typically 100-300 sensors, controllers and electrical actuators connected in analogue and digital networks. Advanced software enables very precise control of all important vehicle functions as well as onboard detection of real and potential failures.
The control of a modern truck diesel engine is carried out by a control unit, Figure 1, located on the engine itself. Cable harnesses are connecting it to engine sensors, injectors and actuators as well as to other control units on the vehicle though CAN networks. In this way, electronics and software enable a very precise and coordinated control of the engine and complete vehicle enabling superior combustion control and fuel efficiency (1). For the electronics, the engine and its exhaust after-treatment system is an exceptionally challenging environment with high vibration level, thermal ageing and thermal cycling over long time.
The electronics need to endure the full truck life-time, i.e. a mileage of 2-3 million km and 30000 to 45000 hours in this environment. In spite of rigorous development and testing, novel and immature electronical solutions often lead quality issues in this extreme environment.
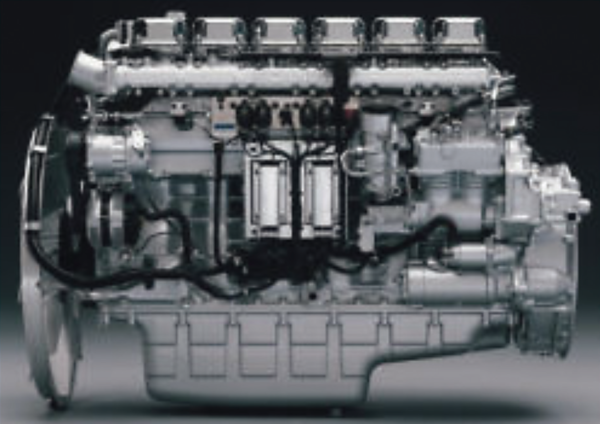
Euro VI and OBD requirements
The legal requirements of engine emissions, Euro 3-6, has led to significantly reduced emissions of NOx and particles as illustrated in Figure 2. In addition, the legal requirements of self-detection of failures to fulfil these emission levels for heavy vehicles during operation (called on-board diagnostics OBD) requires a number of new surveying sensors and software functions. As a consequence, the number of critical electrical components placed on each vehicle has increased.
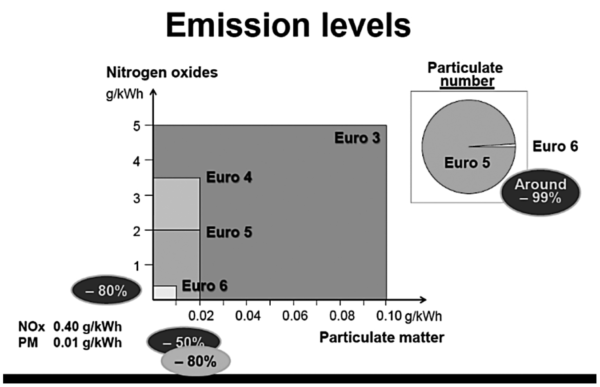
Reliability demands and connected vehicles
Failure of individual components in complex vehicle systems tend to be difficult to understand and are typically linked to the severe environmental conditions. A main concern for vehicles designers is to understand how durable individual components need to be in order to achieve sufficiently high reliability on a vehicle level (2). Using a simplified but effective approach, we may regard all hardware component failures as independent of each other. Statistically, the probability that all parts in a system of n components will function, P, can then be expressed as
where pi is the likelihood that each individual components fails during a given time and <p> is the average failure rate for one component. In Figure 3, the number of failures per vehicle is illustrated for a system consisting of 200 to 2000 components as a function of the average component failure rate per year.
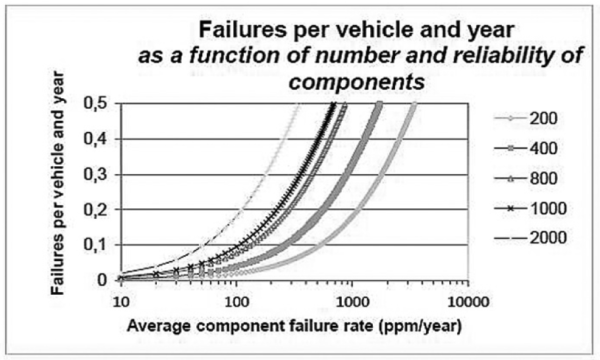
Acceptance levels for vehicle failures during operation are low and decreasing. The costs for a truck standstill are normally huge, since not only repairs costs but the high costs due loss of income and customer confidence also should be taken into account. For the electrical system of a truck with a couple of hundred components, a vehicle failure rate in the order of 0.1 to 0.3 failures per year will require average component failure rates of only 200 to 500 ppm / year, as illustrated in Figure 3.
In order to meet such low component failure rates in real vehicle operation, traditional environmental endurance testing for automotive components needs to be complemented with broad follow-up of component failures from field operation. State-ofthe- art trucks offer the possibility of failure data collection from fleets of connected vehicles. In this way, real and potential failures can be detected early for large fleets also then failure rates are relatively low (3). Good control of how the electronics functions as well as its supporting software will be essential to remain competitive in the heavy vehicle business. In the future, the companies mastering robust electronics in combination with own supporting software will be in a position to offer vehicles with superior functionality and reliability.
Niklas Karpe, Scania CV AB
References:
- Bosch Automotive Electrics and Automotive Electronics, 8th Ed, 2014
- Dimitri B. Kececioglu (Author) Reliability Engineering Handbook: Vol 1, 2002
- Frida Kvarnström, “Statistical methods for lifetime analysis and failure rate analysis”, M.Sc. Thesis, Umeå University, 2013